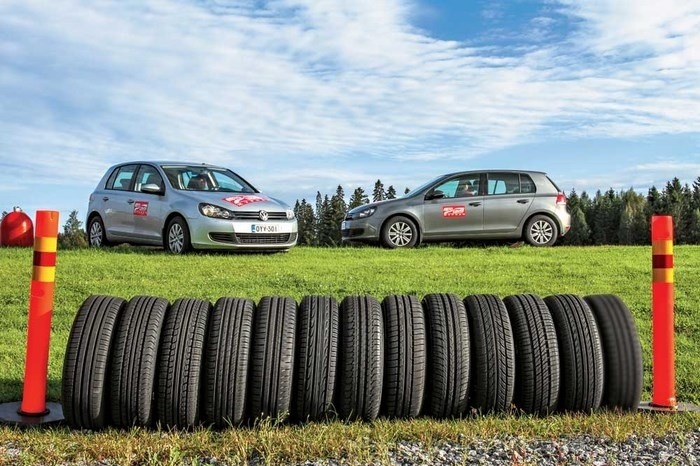
Любой автовладелец мечтает о том, чтобы приобретённые шины (колеса) соответствовали требованиям, которые к ним предъявляются. Если дан, к примеру, гарантийный срок эксплуатации шинам, - они должны отходить именно такой срок, не меньше.
Как же производитель может гарантировать предусмотренные для шин технические характеристики?
Общеизвестно, что только с помощью испытаний, которые демонстрируют все достоинства и недостатки выпущенных протекторов, можно удостовериться в правдивости того, что обещают производители. А фирмы, выпускающие шины на тест-драйвы не скупятся.
Производители устраивают для покрышек дорожные испытания: это и «змейки», и заносы, и торможения, и «переставки». Кроме этого, шины подвергаются целому комплексу стендовых тестов. Сначала это определение наружных размеров. Масса шины позволяет оценить эффективность и экономичность использования материалов для её изготовления.
Обязательные этапы проверки высокоскоростных шин для легковушек на статистический и динамический дисбаланс.
Статический дисбаланс определяет неоднородность масс измерением центробежной силы при вращении и силы тяжести.
Динамический дисбаланс может появиться при неравномерном распределении масс в колёсных плоскостях.
Геометрическая неоднородность шин определяется радиальным и боковым биением шин. Силовая неоднородность протекторов определяется с помощью колебаний радиальной и боковой сил ввиду конусного эффекта. Подсчёт ведётся при одном обороте её вращения. При силовой неоднородности растут потери при качениях. Шина перегревается, в самом худшем случае – разрушается.
Прочность или определение энергии разрушения пневмошин происходит при вдавливании цилиндрического стального плунжера в центр протектора. Оценивается способность шины сопротивляться под воздействием концентрированных усилий, появляющихся в виде неровности при контакте шины и дороги.
Под воздействием упора на боковую часть шины с нарастающей силой до потери её герметичности определяется сопротивление бескамерных моделей сдвигу с полки обода.
На специальной установке проводятся испытания на гидропрочность или гидротест. Шину в специальной камере накачивают водой под давлением до её полного разрушения. Дело в том, что вода, в отличие от воздуха, не сжимается, соответственно, колесо разрушается, не взрываясь. А после взрыва трудно было бы понять причину возможного дефекта. Шины проверяются на герметичность: выясняется, как быстро воздух диффузирует через резину. Согласно методике потери внутреннего давления определяются за срок в 30 суток.
Для определения коэффициента сцепления и жёсткости шин с опорной поверхностью на испытаниях в боковом, угловом и продольном направлениях перемещается опорная плита. Фиксируется усилие сдвига и перемещение плиты.
Специальная сенсорная система анализирует, как распределяется давление в контактном пятне шины и дорожного покрытия. Измеряются и распределение удельного давления под нагрузкой, и само контактное пятно шины и дороги.
Для определения электропроводности шин измеряется электрическое сопротивление или способность к рассеиванию электростатического заряда. Замер делается между шиной на ободе и пластинкой из металла, на которую шина загружается при нагрузке.
Рентгеновскими лучами контролируется правильность сборки покрышки с металлокордом. Это, как правило, применяется и при выборочном заводском контроле. Проверяются они и на сопротивление боковому удару.
Стендовые испытания включают также испытания на скорость и нагрузку. Оценку биения и начало разрушения каркаса позволяет произвести планка над шиной. На стендах проверяется ходимость, а коэффициенты бокового увода и сцепления тестируются в лабораториях специализированных институтов. Заводы таким оборудованием не располагают. Там же, в лаборатории определяется коэффициент сопротивления качению: чем он меньше, тем лучше.
Проверяется, как протектор сопротивляется проколам, а также как работает шина в зоне боковин и борта. Результаты всех проведённых тестов, как правило, подтверждают заданные эксплуатационные параметры.
Неразрушающим видом контроля шин считается интерферометрический метод. Он выявляет пузыри, посторонние включения, расслоения – словом, всё, что не видно глазу. Применяется при освоении новых моделей.
Способов испытаний, как видно, великое множество. Причём, у отечественных испытателей они свои, у зарубежных – свои. Все они, как правило, придерживаются общепринятых методик. Объединяет все испытания шин в России и за рубежом то, что метод замера параметров должен обеспечить не только качественный, но и количественный отбор. Практически одинаков для всех и срок испытаний. Готовая шина может испытываться около двух месяцев.
Отдаю предпочтение импортным производителям. Несколько лет езжу на японских шинах и полностью доволен их качеством. Причем это касается и летних, и зимних шин, которые меняю весной и осенью, ведь в наших условиях ездить на одних и тех же невозможно.
Сегодня ведущие мировые производители шин настолько скрупулезно относятся к качеству своих шин, что автовладельцы могут быть спокойны - их шины прослужат много лет и не подведут в любых дорожных и погодных условиях.
Предпочитаю лучше взять пару покрышек известного производителя и быть уверенным в качестве, чем купить 4 колеса отечественных.
Хоть наши, хоть импортные производители никогда не признаются, если выпустят шины просроченные, то есть с меньшим проходом. Если напишут, что гарантия на шину месяц, так её не купит никто, пусть и дёшево.
Вроде бы стараются предусмотреть все, что может случиться на дороге. И забота радует. А вот интересно, китайцы проводят такие же дотошные испытания по всем параметрам или дешевизна не предусматривает стопроцентной надежности в любых условиях?
Я не уверен, что прямо все производители проводят испытания столь серьезные. На Западе, вполне возможно, в странах с более низким уровнем развития - едва ли.
Зимний комплект у меня Bridgestone, а летний Michelin. Отлично ведут себя в самых разных ситуациях - дождь, гололед, гравий, песок, снег. Считаю, что правильный выбор покрышек - одна из основ безопасного вождения.